Whether you're developing a medical device, a consumer-level wearable, or a connected IoT gadget, there's a good chance that it will require some form of signal conditioning. Signal conditioning is the interface between the product's sensors and data acquisition hardware. The conditioning circuit plays an integral role in the overall functionality of your device, rendering many of its advanced features possible.
Because so many types of sensors exist, conditioning circuits come in a wide range of specifications. While it's an often-overlooked component, having a basic understanding of how the conditioning process works can make all the difference during the development of your product.
Signal Conditioning Explained
First things first: What is signal conditioning, and how does it work?
The sole purpose of signal conditioning is to take the signals from the sensors and prepare them for further processing. The electronic circuit integrates into a more extensive data acquisition system, also known as a DAQ.
Sensors pick up real-world environmental or mechanical phenomena, such as vibrations, temperature, and more. Those signals are analog, and they need to be digitized to be read. The job of the DAQ is to sample and measure the data, turning it into a digital format that computers and software can manipulate, store, analyze, and display.
The issue with the data acquisition process is that raw signals are subject to many quality problems. The signals can be very small. They may not be linear. They may lack calibration. Alternatively, they could have noise.
Whatever the case may be, signal conditioning works to correct these deficiencies. It makes the signal ready for the next stage of data acquisition, ensuring accurate and useful data.
Common Conditioning Techniques
The accuracy and overall efficiency of the DAQ system in your device depend entirely on the signal conditioning design. There are many ways to prepare the signal for processing.
The following are common ways that signals need to be processed.
-
Amplification
In many cases, the analog signal has too tiny an amplitude to feed into the DAQ system. Not only does it make the signal more susceptible to noise and interference, but the system might not detect the data at all.
An analog-to-digital converter or DAQ may need an input signal that is 3- or 5-volts full scale. Many signals are only millivolts. An amplifier is required to boost the signal. The amplifier is most often single-ended, with a single input referred to as ground. Some amplifiers are differential, measuring the difference between two inputs. This is needed when the signal is not referenced to ground or for small signals where the ground reference is noisy.
-
Linearization
Linearization is a common signal conditioning task for temperature measurements and many other signals.
It applies to any signal that doesn't have a linear relationship between the signal value and the physical quantity it measures. Take thermocouples as an example. They have a nonlinear temperature-to-voltage relationship.
There are circuits that provide linearization for certain common sensors, such as thermocouples. For other signals, the linearization is now usually done after the signal is digitized.
-
Excitation
Excitation is the process of delivering power to the sensor. Active sensors require external voltage or a current to operate. A signal conditioner provides the excitation source. Many kinds of sensors need this form of conditioning. Some examples include resistance temperature detectors, strain gauges, and pressure sensors.
The output signal is proportional to the voltage input for many of these sensors, so the signal changes when the power input changes. The source must be very stable over time, temperature, and load to get an accurate measurement.
-
Cold Junction Compensation
This type of conditioning is specific to thermocouples. A thermocouple sensor relies on the Seebeck effect, which is a relative temperature. It is relative to the junction where the thermocouple connects, called the cold junction.
A separate sensor measures the cold junction temperature. The actual temperature is what the thermocouple reports, plus the cold junction temperature.
-
Isolation
Electrical isolation separates the circuit from the other sources of electrical potential, ensuring external voltages don't affect the sensor readings.
For example, a thermocouple mounted to a motor's windings may contact high voltage wires. To prevent damage and make accurate measurements, you would electrically isolate the amplifier from the thermocouple. However, isolation is not often used, especially in battery-operated devices, because it is expensive.
-
Sampling Errors
The above signal conditioning has to do with the amplitude of the signal. When a signal is digitized, you also must pay attention to the timing. Digital signals are discrete, not continuous, so the sample rate is important. You usually don't have to pay attention to the sample rate for some signals, such as temperature. Others, such as vibration, are critically sensitive.
The digitized signal will not represent the analog signal if the vibration frequency is faster than the sample rate. Sampling theory says the sampling rate must be at least twice the highest frequency in the signal to avoid aliasing. You sometimes see this effect in a movie where the wheels on a vehicle appear to run slowly or even backward. This happens when the movie's frame rate is close to the rate of motion of the wheels.
A filter is usually used to eliminate frequencies more than half the sampling rate. In actual practice, because filters are not perfect, removing frequencies much lower than half the sampling rate is necessary.
-
Simultaneous Sampling
If two signals are being measured and compared in time, they must be sampled simultaneously. Most analog-to-digital converters sample one input channel at-a-time, so there is a time difference between each channel.
For signals such as vibration, it is often important to avoid the time difference. A simultaneous sampling circuit is used to capture all the inputs at the same time. Then the analog-to-digital converter can read them one at a time.
Accurate and Reliable Data Acquisition with Signal Conditioning
Sensor signal conditioning is crucial for proper data gathering. These small but mighty components are an indispensable part of DAQ systems. But like all complex electronics, the design and implementation are what matters most.
If you're not sure how signal conditioning fits into your device, turn to Voler Systems. Specializing in sensor technology, we can ensure project feasibility and DAQ accuracy through proper design.
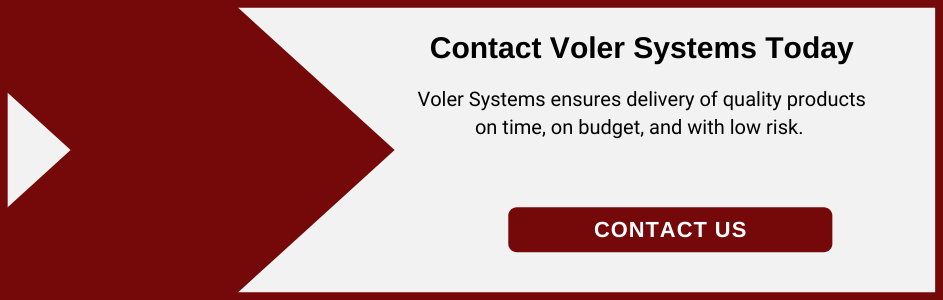