How We Work
*Walt Maclay, Founder of Voler Systems and Chairman of the Board, hosting some visitors at the Sunnyvale CA offices
Our technical team spans all the stages of new product development, from conceptual design through manufacturing transfer and regulatory compliance for a wide variety of clients and markets. One of the most important values that we offer to you is to identify and communicate risks as the project progresses.
Voler Systems delivers quality products, on time, on budget, with low risk. We make sure our customers are successful by using a proven process that includes the following.
Evaluate the proposed product and identify the key challenges
We first strive to understand your needs and limitations. What is most important for you? Is it time-to-market? Is it getting a prototype at low cost? We look for ways to meet your needs and keep risks low.
When a risk is identified, we have ways to reduce the risk. The most important is to address the risk as early as possible. Sometimes a feasibility investigation is required to determine if a particular design idea will work. The feasibility investigation is done before any design work.
In the past, we have sometimes determined that the design approach needs to be changed for unanticipated reasons as a result of the feasibility investigation. This has saved significant money by avoiding problems early or not developing the wrong thing.
We strive to ‘over-communicate’ to your team and among ourselves. Many of us, particularly engineers, tend to under-communicate and not give a clear picture of the project status. Many of you have known an engineer who under-communicated.
So to compensate, we strive to over-communicate what we are doing. We use this over-communication tactic both in writing as well as verbally. Since everybody has different ways of communicating, we use a combination of verbal and written communication to help get the message across clearly.
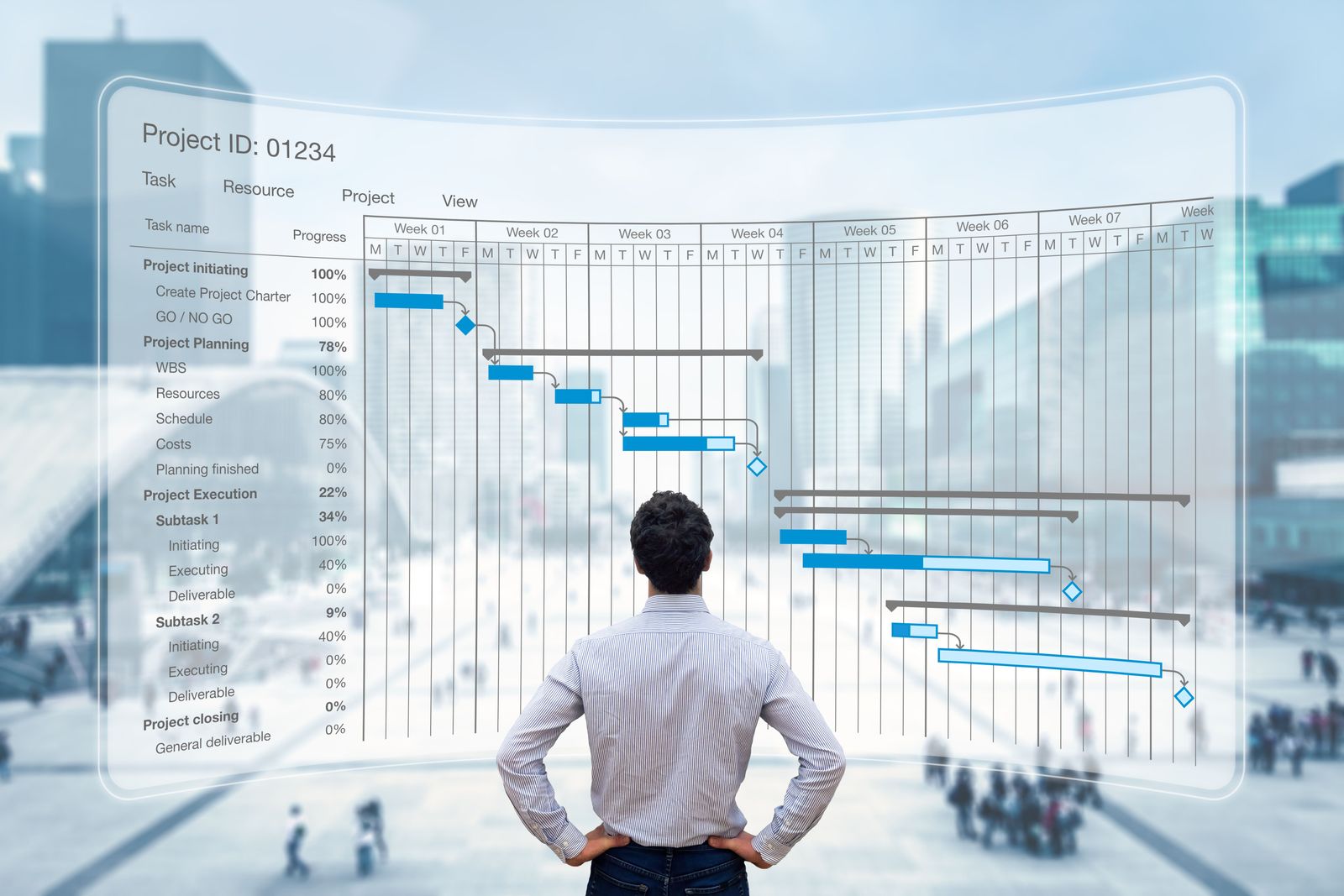
Develop an architecture and make sure requirements are complete and accurate
We invest a lot of effort in getting clear and complete requirements at the beginning of a project to ensure our team is all on the same page with your team. We often help our clients develop the requirements.
We may iterate several times with you to make sure that we have a complete understanding of your objectives and the constraints of the design problem. Although this may seem like a slow way to start, we have found this is the best way to ensure you get what you are asking for.
We have found through our experience that this small amount of effort invested in clarity and completeness up front will prevent many problems from cropping up as the project progresses.
The schedule and the quality of the final result depend on a complete understanding of your needs and objectives upfront. The specification will drive not only our initial approach and decisions but many of our subsequent ones as well. We can make the best choices on your behalf when you invest some time upfront to accurately scope the desired performance, cost, and quality of your design.
Here are two guides to help you write a requirements document:
We then do a high-level design called an architecture. We create a block diagram, and we may select some key parts. We evaluate risks and how to mitigate them.
One task we often help clients with is exploring the feasibility of developing an idea into a product. Sometimes it is not clear that an idea can be implemented, or it is not clear how to implement it.
A feasibility stage is a short investigation to determine how the design should best be done. We view our role as working with customers to explore the many possibilities for improvements or enhancements in their specific market niche. We identify solutions that work to save time and money. We develop solutions to meet business needs.
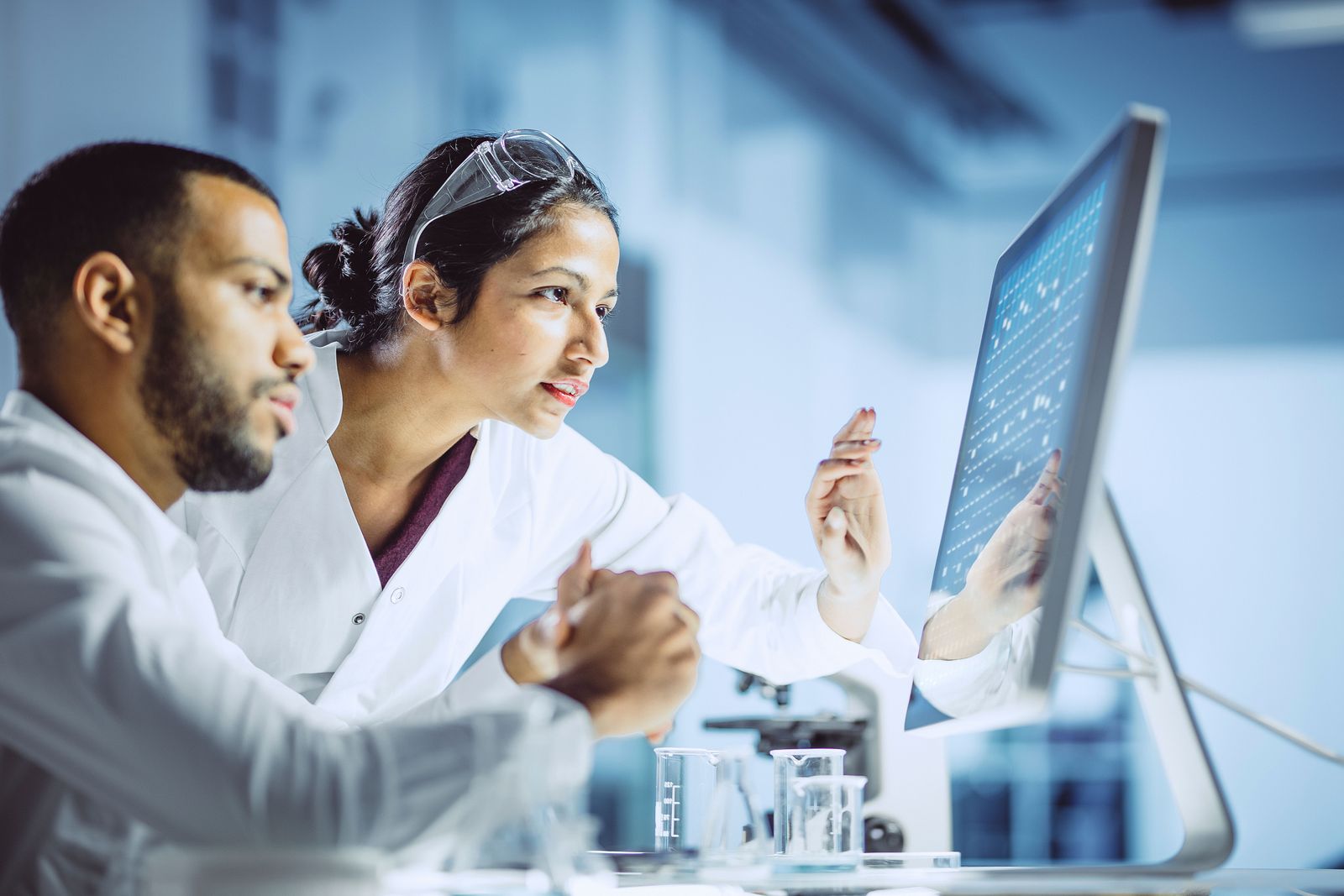
Assign the personnel, partnerships and skills needed to execute the project
We assign engineers with the right skills, and we have a project manager who ensures the project is on time and on budget. The project manager is responsible for maintaining good communication with you.
A successful project requires the communication and collaboration of key stakeholders. We strive to get buy-in and collaboration from all key stakeholders early in the project. We realize that our communication is not just limited to one narrow chain of command, but instead, we understand all the dotted lines of support that engineering provides for typical project teams.
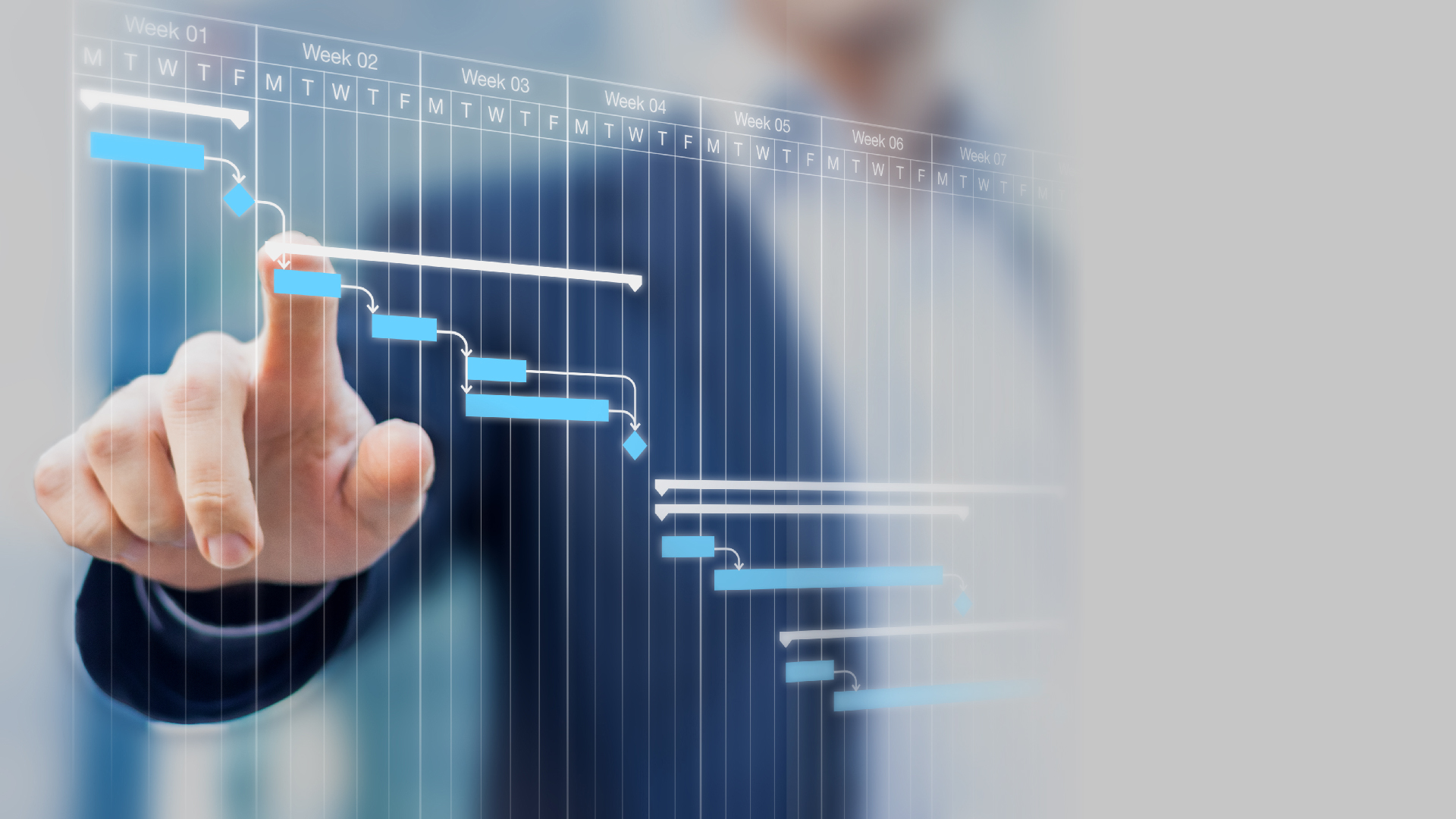
Report on progress weekly concerning budget, schedule and technical topics
We have a weekly meeting between your team and our team. In the meeting, we discuss the status, technical challenges, and anything else that will help keep you informed and move the project forward on schedule and on budget.
We have a weekly meeting of our own management team. Each week, we review the project status among ourselves.
Communication is not what’s said but what’s understood. We may sometimes ask you to repeat what you have heard from us, and we communicate back to you our understanding of what you have instructed us to do.
This helps ensure that we both understand not only the project’s specification but what the current status is, what risks we have identified and our plans to manage them, and what the current schedule is for completion. As we repeat this back and forth, we both begin to gain a more in-depth understanding of the project at hand.
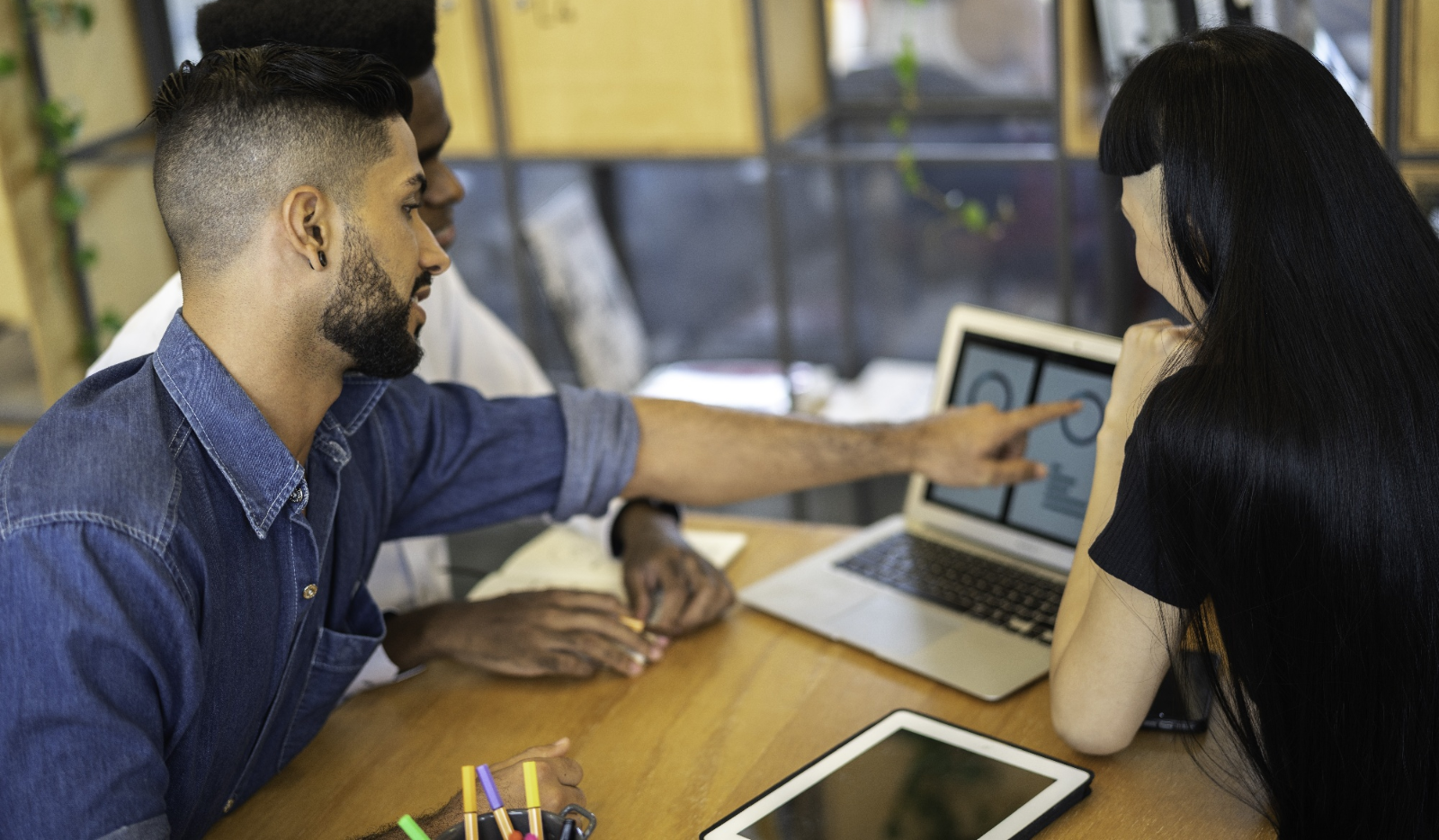
Coordinate participants in the engineering arena
An important outcome of the meetings with you and our internal meetings is the coordination of the work with you and any others working on the project. Keeping people working effectively together requires good project management.
For example, when designing a circuit board, we typically need to work with the mechanical design team interactively. We give each other our design criteria, then adjust to find the best compromise.
Selecting parts has always been very important, and now it is more critical than ever. Once the design is done, you need to be able to purchase the parts for a long time. Due to supply chain problems, some parts are hard to get, and some become suddenly unavailable.
There are several strategies to minimize these problems. We can check on what the manufacturer says about the parts. They give notice well in advance before stopping manufacturing. We can design with the ability to substitute parts if one becomes unavailable. Sometimes the best strategy is to purchase key parts in advance.
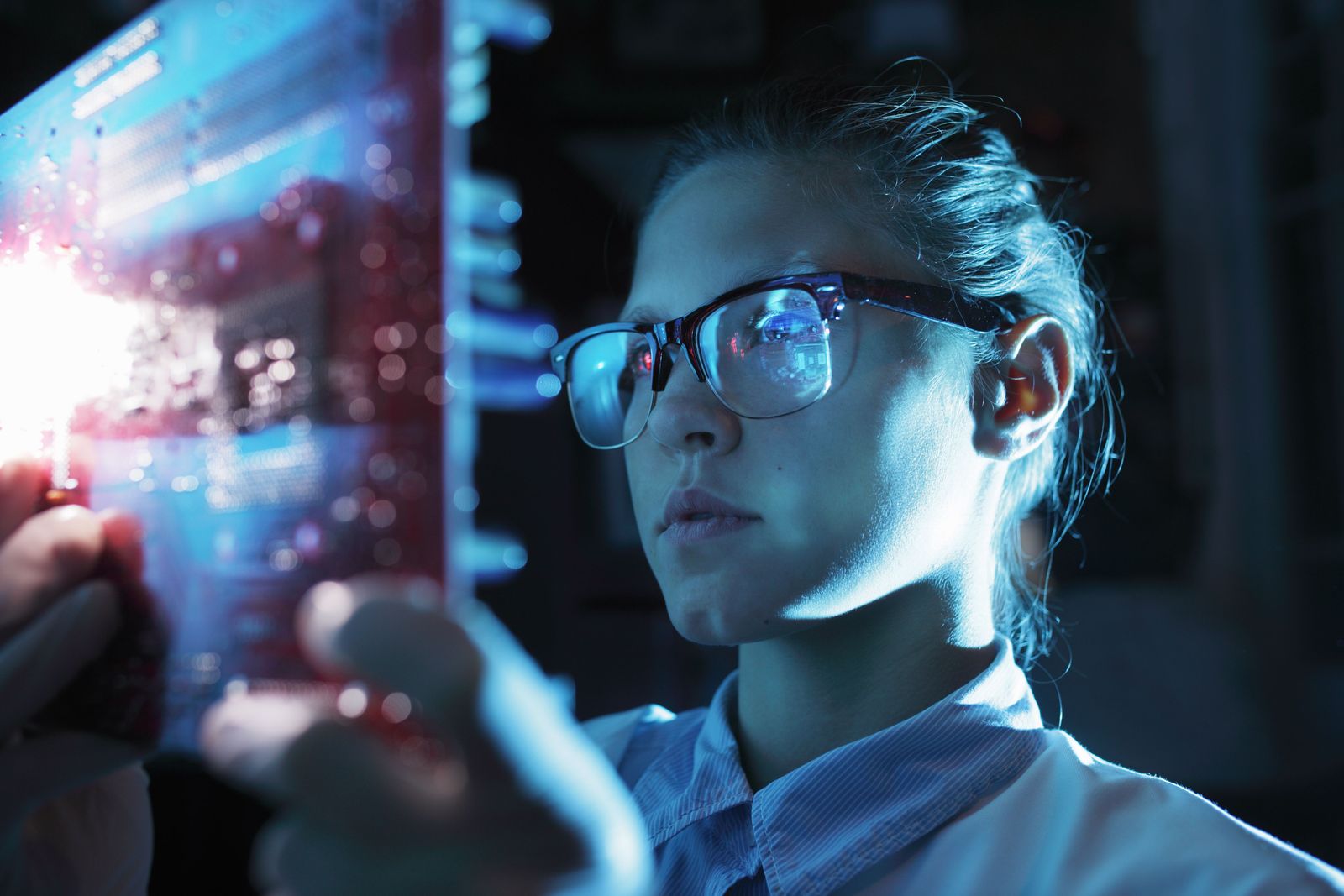
Handle first prototype fabrication and first test of hardware/firmware
This phase includes detailed electrical design, firmware development, and working prototype fabrication. We then test the prototypes to make sure the design is done correctly. You can then evaluate the prototypes and even try them with selected customers.
At this point, the design is done, and there is complete documentation, but changes are likely needed before starting manufacturing. The testing that is done will likely uncover things that need to be changed, and some changes may need to be done to make the product more easily manufactured. That is the next step.
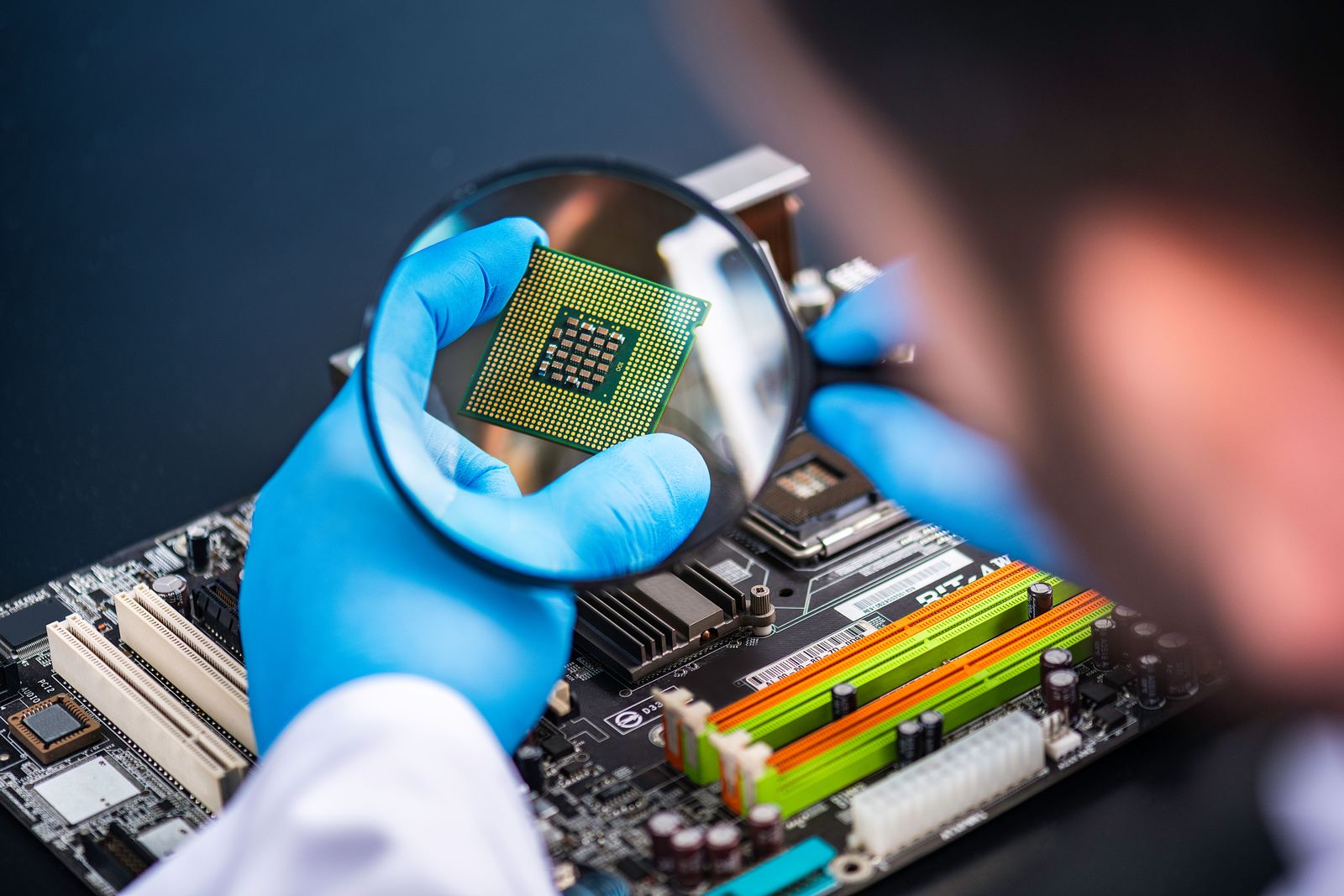
Define debug updates, regulatory certification, manufacturing and system test
In addition to testing that the hardware and software function correctly, we also do compliance testing to make sure the design meets government regulations for things such as emissions and safety. Medical devices need additional testing called verification and validation. We can do this work or work with you to ensure others are completing it.
We work with the manufacturer to ensure the design can be easily manufactured in their process. Each manufacturer has a process that is a little different. Electronic products need to be tested before they are sent to customers. The design company needs to work with the contract manufacturer to decide how the product will be tested and to design in ways to test it adequately. This is called Design for Test (DfT). Failing to follow these steps thoroughly has caused companies serious loss of money and market share.
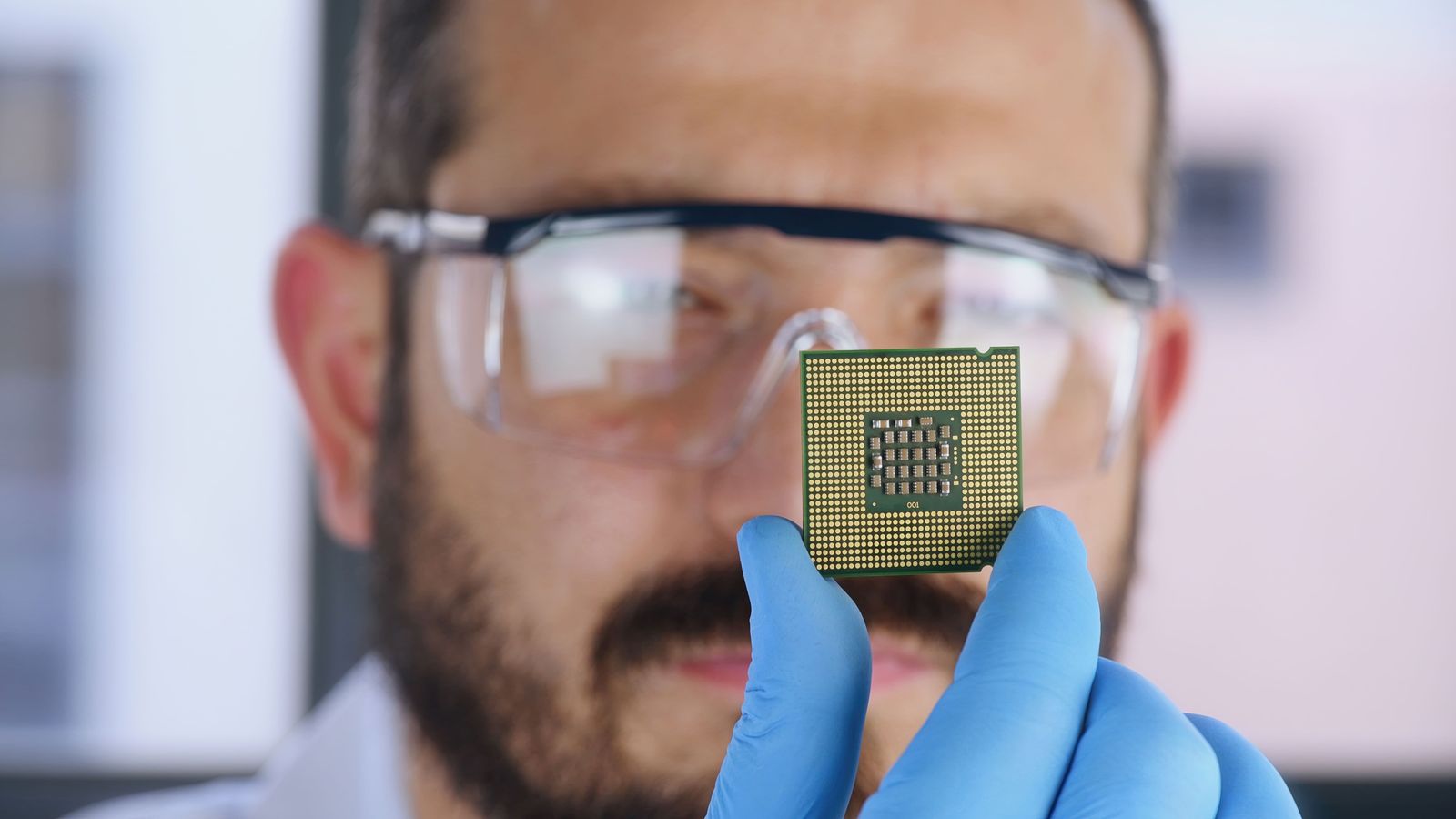
Complete design for manufacturing and documentation
Design for test, design for manufacturing, develop a production test, and complete the documentation. Some products need carefully written assembly instructions. They must be written so a non-technical person who does not know English very well can follow them easily.
When designing a product, the designer must take into account that all the parts will not be exactly the same. There is variation from part-to-part. The product must work well with any of these parts. Making one prototype that works properly is not enough. Calculations must be done to verify the product will work with any combination of parts.
There are other strategies, such as Design for Reliability (DrR), which are important as well. The product can be tested over the temperature range, humidity range, altitude, and mechanical shock (such as dropping it) to which it will be subjected in normal use.
.jpg)
Deliver data and documentation that is proven and ready for use
With careful design and transfer to manufacturing, you can have highly successful product launches and smooth production. For example, we recently designed a consumer product that went quickly into volume production.
In less than six months, they made 500,000 units. There were only 500 that didn’t work (0.1% failure rate). This success can only happen when all the design and manufacturing steps are done carefully and teams work together.
It is crucial to work with experienced designers who know how to transfer a product into production and to select a manufacturer that can build the product well.
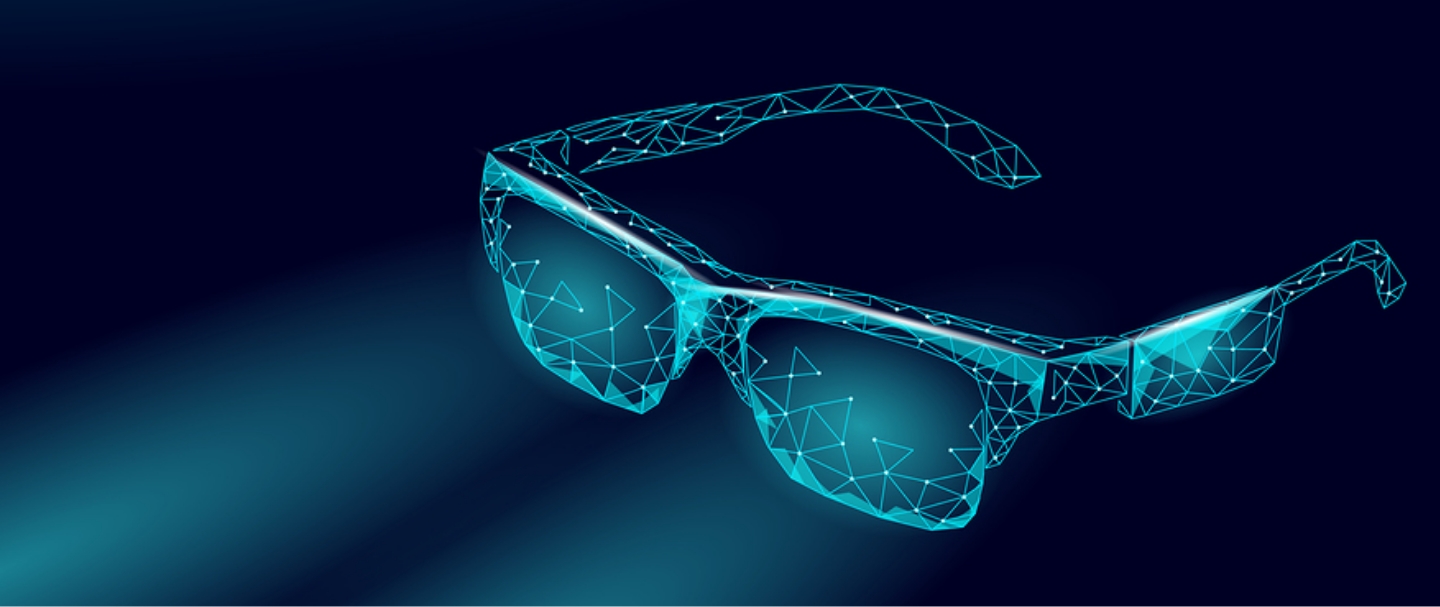